Your industrial hose supplier should be aware that tube erosion (typically called the popcorning) in steam hose is most pronounced in hoses on the market which have tube of inferior rubber. The popcorn effect is what destroys a steam hose and the steam network. It is also what can injure workers when a hose fails. Popcorning destroys steam hose from within and the effect occurs when:
- Microscopic water particles collect in the wall of a hose. When new steam enters the hose it heats up those particles, which expand explosively to 1600x their size.
- When that happens, popcorn-like blisters explode on the hose’s inner surface. The resulting particles of rubber can contaminate the steam network or the product.
- Over time, moisture forces its way out towards the skin of the hose, weakening the steel braiding and making it unsafe for use.
The popcorn effect is most pronounced when hoses are built with an inferior tube compound.
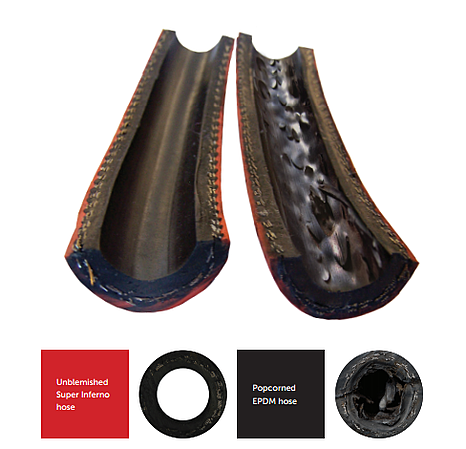
To prevent blistering or popcorning on the inner surface of steam hose, Goodall® formulated a premium, proprietary Chlorobutyl compound that's 15x less permeable than EPDM. Even after thousands of hours of stop-start use, the Super Inferno, Inferno, and Dante hose shows no signs of popcorning. The lower the permeability, the longer the hose life, the greater the safety.
The Goodall range of Chlorobutyl hoses are:
- Made of an abrasion and ozone-resistant EPDM in a distinctive red and black spiral striping for high visibility in all situations
- The hose inside is pinpricked to significantly reduce the likelihood of cover blisters
- Inside, multiple high tensile wire braids add plenty of integrity to handle a maximum pressure of 250 PSI at temperatures ranging from -40°F to 450°F
Goodall also formulated a high grade EPDM tube compound that provides excellence resistance to the effects of popcorning, resulting in durable, long-lasting steam hose assemblies.
Click here to complete a form download a technical datasheet for more information on the Goodall® steam hose products.